Application of Wall Coatings
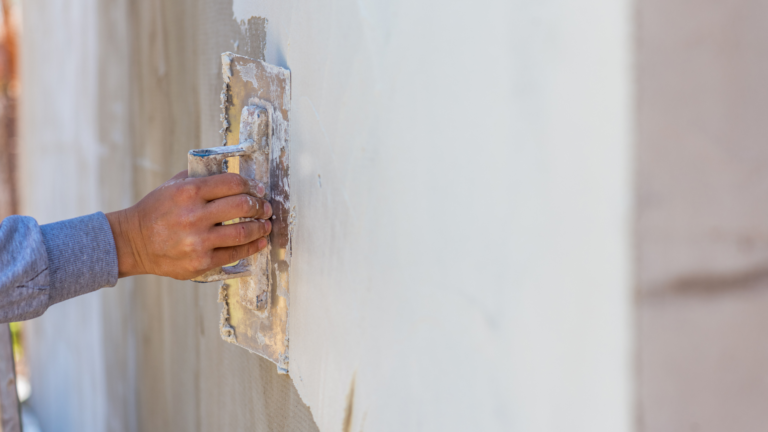
Wall coatings are an essential part of the waterproofing system and the building envelope. Various factors should be taken into account when selecting a wall coating, whether it is for a new project or for a restoration or re-coating application.
Preparing the surface is extremely important. The substrate (concrete, masonry, stucco, etc.) or surface (another wall coating) should have no holes or cracks, free from dirt and debris, and dry with a manufacturer specific moisture content.
Generally, a coating is made up of four primary ingredients: Binder, Pigment, Carrier, and Additives. The binder is the film forming portion, and can be acrylic or silicon, among other types. The pigment is the color. When exposed to sunlight, bright (organic) colors tend to fade quicker. Coatings can also be elastomeric or non-elastomeric. Elastomeric coatings are more flexible but may be less durable.
A mock-up should always be performed to ensure the selected coating performs as intended. Adhesion tests, per ASTM D3359, should be conducted in multiple locations to ensure the coating is adhering as intended. Lastly, the coating should be applied properly (both in wet mil thickness and application technique), whether by roller, power sprayers, or paint brush.
Wall coatings can provide protection for your building in the form of waterproofing, weatherproofing, or insulation, so it is critical for the application process to be done correctly. The team at Burby Engineering is experienced in evaluating paints and waterproofing coatings on buildings and specialty structures such as elevated pools, terraces, balconies, wall systems and parking garage structures. For more information or for a consultation on your issue, please contact us at info@burbyengineering.com or call 813.600.3339.