Low-Slope Roof Drainage Systems
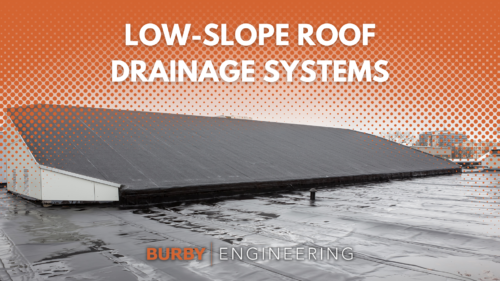
To ensure the successful performance of roof coverings on low-slope roofs, the roof drainage systems must be designed and installed properly. On low-slope roofs, water is not designed to drain over the roof’s edge, unlike conventional sloped roofs. Roof drains and scuppers should be placed at the low points of the roof and sized to convey the water at the building code required mean recurrence interval. The flashing at drains and scuppers is a significant detail since these areas will experience excessive amounts of water by design. Water intrusion, or even roof collapse, can occur if there are improperly located and inadequately flashed roof drains and scuppers.
Roof drains should be installed in sump areas, which are usually created by tapering the underlying insulation towards the drains. There should not be any seams of the roofing membrane located within sump areas. To prevent water intrusion, the roof drains must be fitted with compression clamping rings. The drain bowl should be to property attached to the drain pipe below. In re-roofing projects, it’s important to ensure the drain bowls do not get disconnected from the drain line when the original roof is being removed. Strainer baskets should be added to prevent blockage. Installation of primary drainage scuppers should be level with the roof surface at the lowest elevations along parapet walls, whereas overflow scuppers should be installed not less than 2 inches and not more than 4 inches above the roof covering. Pre-fabricated scupper inserts should be used for flashing.
These are just general recommendations for the installation of low-slope roofs. To ensure proper installation, follow the procedures outlined in the roofing manufacturer’s published instructions. Not only will following these details be critical for the proper installation of the product but it is also required by the building code. Furthermore, the building code requires that testing be performed on the drainage and vent system to determine compliance with the provisions of the code.
Burby Engineering, Inc. can assist in roof design, testing, and inspections, or building code-related issues. Contact us for more info!